Ideal Practices for Preventing Weld Undercut: Mastering the Essentials
Ideal Practices for Preventing Weld Undercut: Mastering the Essentials
Blog Article
A Comprehensive Overview to Identifying, Averting, and Dealing With Undercut Welding Troubles in Your Welding Projects
In the realm of welding, encountering undercut concerns is an usual challenge that can jeopardize the architectural honesty and general quality of your welding jobs. Stay tuned as we explore the essential components of recognizing, avoiding, and repairing undercut welding problems, offering you with beneficial understandings and strategies to elevate your welding skills to the next degree.
Typical Reasons For Undercut Welding
Undercut welding, an usual problem in welding procedures, can be triggered by various elements that need to be carefully recognized and dealt with to make sure the integrity of the weld joint. One of the key reasons of undercut welding is extreme warm input.
An additional typical cause of undercut welding is improper welding method. Recognizing these root triggers and applying restorative actions is essential in preventing and fixing undercut welding issues in welding tasks.
Identifying Undercut in Welds

To recognize undercut precisely, proper lights and magnifying devices are crucial to check the weld joint completely. Using tools such as a welding gauge or a magnifying glass can help in detecting even the tiniest undercut blemishes. In addition, running a finger or a fingernail along the weld joint can occasionally reveal undercut, as the surface area might really feel irregular or have a dip where the undercut exists.
Safety Nets for Undercut
Having a deep understanding of the reasons for undercut in welds permits the application of reliable safety nets to maintain weld quality and honesty. One critical safety net appertains weld joint preparation. Making certain that the edges are clean, without contaminants, and correctly beveled can dramatically minimize the probability of undercut (Preventing weld undercut). In addition, selecting the suitable welding criteria, such as voltage, present, and take a trip speed, is essential. These settings need to be enhanced to stop too much warmth input, which can cause undercut formation.
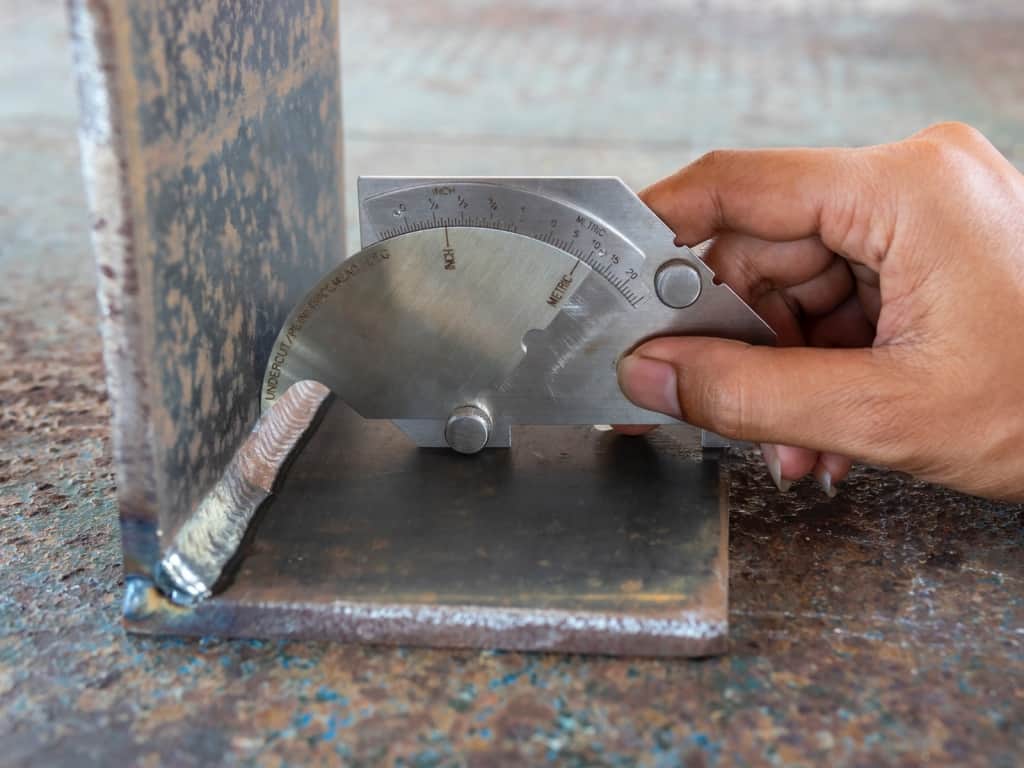
Techniques for Fixing Undercut

Enhancing the welding existing or reducing the travel speed can help fill up in the undercut. Furthermore, changing the welding technique from a push to a drag or vice versa can also aid lessen undercut.
One more strategy is to use a weaving motion while welding to guarantee appropriate sidewall blend and fill in the undercut. By oscillating the welding arc from side to side within the weld joint, the welder can transfer more filler product right into the undercut locations, efficiently getting rid of the flaw.
Additionally, grinding out the undercut and rewelding the joint can be a practical service for more extreme undercut problems - Preventing weld undercut. This procedure entails eliminating the undercut section, preparing the base steel, and after that rewelding the joint with appropriate welding criteria address and strategies to prevent undercut from repeating
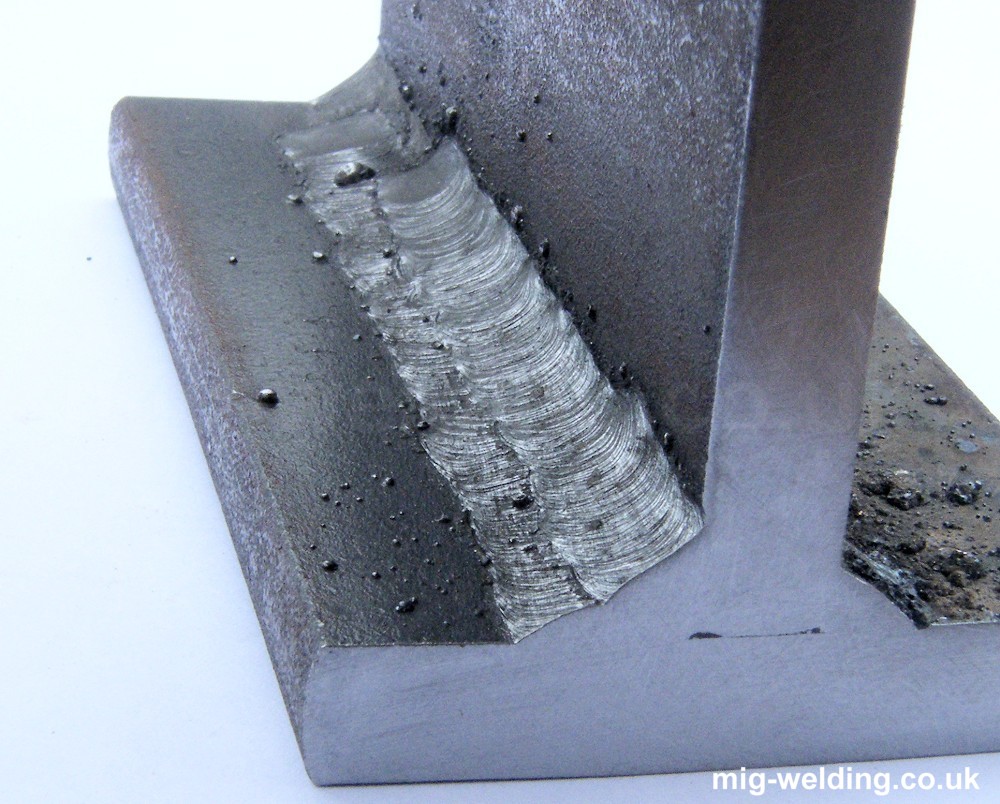
Specialist Tips for Staying Clear Of Undercut
Utilizing correct welding techniques and maintaining control over crucial welding parameters are crucial approaches for welders aiming to stop undercut in their weld joints. One specialist pointer for avoiding undercut is to guarantee proper joint preparation. This entails cleansing the base metal extensively to remove any type of impurities that could lead to undercut development. Additionally, picking the proper welding process and filler steel for the click to read particular application can assist protect against undercut. Welders should likewise pay attention to the welding current and voltage settings, guaranteeing they are within the suggested range to stay clear of overheating and possible undercut. Preserving a consistent traveling rate throughout the welding process is an additional important idea to protect against undercut. By moving at a steady pace, welders can make sure proper blend and lower the chance of undercut formation. Finally, examining the weld grain after completion can help recognize any indicators of undercut very early on, permitting immediate restorative action to be taken.
Verdict
Finally, identifying, stopping, and fixing undercut welding troubles in your welding tasks is essential for making sure solid and resilient welds. Preventing weld undercut. By understanding the common sources of undercut, being able to recognize it in welds, applying precautionary measures, and utilizing proper techniques for taking care of undercut, you can stay clear of possible problems and produce top notch welds. Adhering to expert ideas for preventing undercut can aid you enhance your welding skills and create much better results in your tasks
Undercut welding, an usual concern in welding processes, can be triggered by different variables that need to be meticulously recognized and dealt with to make sure the integrity of the weld joint. Furthermore, running a finger or a finger nail along the weld joint can often reveal undercut, as the surface may feel unequal or have a dip where the undercut exists.
Making use of proper welding strategies and keeping control over crucial welding parameters are important techniques for welders intending to stop undercut in their weld joints.In verdict, identifying, protecting against, and fixing undercut welding troubles in your welding projects is critical for guaranteeing long lasting and solid welds. By understanding the usual causes of undercut, being able to identify it in welds, carrying out precautionary steps, and utilizing appropriate strategies for repairing undercut, you can stay clear of possible problems and develop high-quality welds.
Report this page